一、电泳涂料成膜原理
1. 涂料工作原理
电泳涂装(electro-coating)是利用外加电场使悬浮于电泳液中的颜料和树脂等微粒定向迁移并沉积于电极之一的基底表面的涂装方法。电泳涂装的原理发明于是20世纪30年代末,但开发这一技术并获得工业应用是在1963年以后,电泳涂装是近30年来发展起来的一种特殊涂膜形成方法,是对水性涂料**具有实际意义的施工工艺。具有水溶性、无毒、易于自动化控制等特点,迅速在汽车、建材、五金、家电等行业得到广泛的应用。
电泳涂装属于有机涂装,利用电流沉积漆膜,其工作原理为“异极相吸”。
电泳涂装**基本的物理原理为带电荷的涂料粒子与它所带电荷相反的电极相吸。采用直流电源,金属工件浸于电泳漆液中。通电后,阳离子涂料粒子向阴极工件移动,阴离子涂料粒子向阳极工件移动,继而沉积在工件上,在工件表面形成均匀、连续的涂膜。当涂膜达到一定厚度(漆膜电阻大到一定程度),工件表面形成绝缘层,“异极相吸”停止,电泳涂装过程结束。整个电泳涂装过程可以概括为以下四个步骤:
●电解:水的电解
●电泳:带电的聚合物分别向阴极或阳极泳动的过程 ●电沉积:带电的聚合物分别在阴极或阳极沉积的过程
●电渗:沉积的电泳涂膜收缩、脱去溶剂和水,形成均匀致密的湿膜 电极附近主要的化学反应如下表所示:
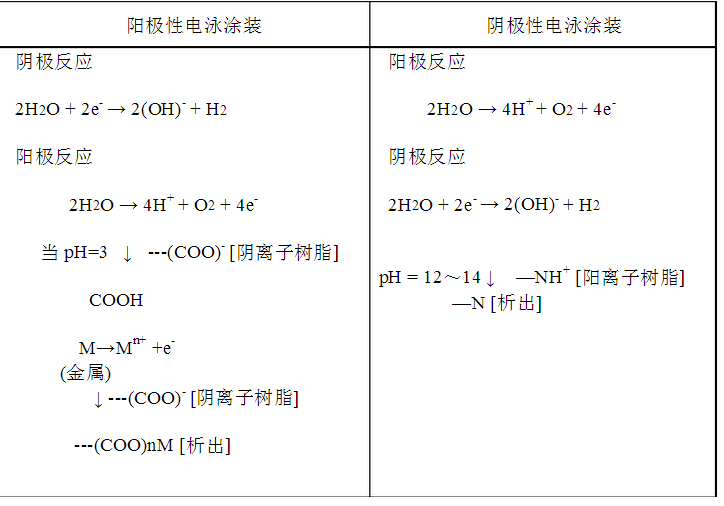
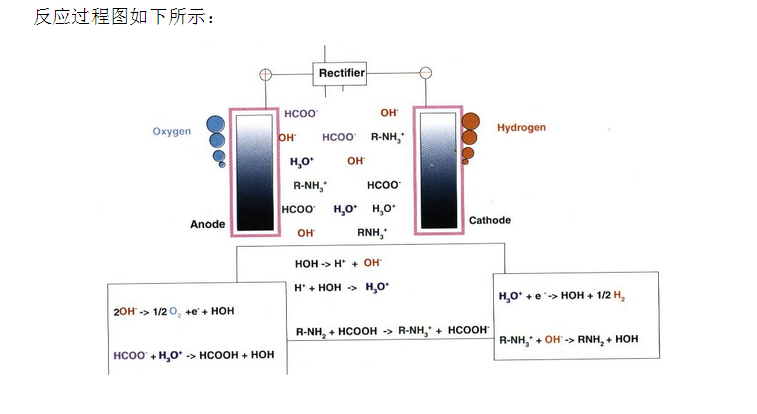
在电场作用下,涂料粒子向阴极移动(电泳),由于受到阴极附近碱扩散层(OH-)的影响,涂料粒子在阴极聚结(电沉积)。槽液的流动影响扩散层,流动速率高,扩散层薄,流动速率低,扩散层厚。刚沉积的湿膜含有大量水分,由于电流的影响,会发生部分脱水,使湿膜不挥发份达到80%(电渗)。脱水后湿膜牢牢黏附在底材上,通常的清洗不能洗脱。由于边缘电流密度高,电泳过程首先发生在这些区域。如下图所示:
2. 电沉积类型
● 阳极电沉积(AED)
阳极电泳涂装,金属工件为阳极,吸引漆液中带负电荷的涂料粒子,电沉积时,少量的金属离子(阳极氧化)迁移到涂膜表面,对涂膜的性能造成影响。阳极电泳涂料主要用于对耐蚀性要求较低的工件,是经济型涂料。 ● 阴极电沉积(CED-cathodic electro deposition)
阴极电泳涂装,金属工件为阴极,吸引漆液中带正电荷的涂料粒子,由于被涂工件是阴极而非阳极,进入涂膜的金属离子大大减少,从而提高了漆膜性能。涂膜优良,具有优异的耐蚀性能。
二、电泳涂装过程
整个电泳涂装过程可分为四个部分: ● 前处理 ● 电泳 ● 后冲洗
工件脱脂后,经过表调、磷化,使表面形成一层均匀致密的磷化膜为进入
电泳槽作准备。 进入槽液,在工件和对应电极间通直流电。在电场作用下,涂料粒子被吸附到工件上并在表面沉积。漆膜达到一定厚度,电泳停止。此时把工件从槽中取出,经后冲洗冲洗掉浮漆,**后送入烘箱固化。 1.前处理
金属工件经脱脂,酸洗除锈(若必要),表调,磷化处理为下一步电泳做准备的过程称为前处理。为了获得良好的电泳涂膜,清洗和磷化都是非常重要的环节。磷化通常采用铁系和锌系磷化液,处理工艺包括喷淋和浸渍。主要适用于钢铁底材。 前处理简单步骤可表示如下(钢铁件为例):
预脱脂→脱脂→水洗→除锈(如有必要)→去离子水洗→表调→磷化→去离子水洗 2.电泳
工件经前处理后进入
电泳槽液,工件入槽前状态必须保证工件表面无油无锈,磷化膜均匀工件表面温度应在40℃以下,进入
电泳槽前工件应全干或全湿,干湿不匀可导致漆膜产生花纹或斑痕。
电泳槽系统各部件及其作用:
● 直流电源(整流器)—提供直流电,使电沉积得以进行。
● 主循环系统—包括循环泵、喷射管以及过滤器,保证槽液混合均匀,同时去除槽液中颗粒污染物及杂质。● 超滤系统—控制槽液电导率,提供后清洗工件的超滤液,并回收浮漆。 ● 热交换器—控制槽液温度。 电泳槽相关系统的控制: 3. 后冲洗
工件从超滤液出来后,利用超滤液冲洗掉黏附在漆膜表面的浮漆,浮漆可以回收到槽液中,使漆液利用率提高,同时保证了漆膜光滑、美观。通过循环系统,清洗液也回收到槽液中,从而使涂装效率达到95%以上。
采用封闭式循环清洗,可以有效去除和回收浮漆,使漆液利用率**大。通过超滤得到的超滤液(含有去离子水、溶剂等低分子量物质)是构成清洗液的**重要的组成部分。
清洗区包括一系列单独的喷淋清洗间或浸渍清洗间。前几道采用超滤液清洗,**后一道采用新鲜去离子水清洗。每道清洗之间都有足够的排液时间。经过**后一道冲洗后,可回收几乎所有的被洗出物。大部分电泳涂装线在工件进入烘房前,利用自动空气吹干机除去漆膜表面的水分,防止水迹产生。 4. 烘干固化 #p#分页标题#e#
清洗吹干后,工件进入烘房,漆膜通过交联固化达到**佳性能。不同的电泳涂料所用的烘烤温度不同,在指定工艺温度下,通常**少需要20min的烘烤时间。大部分烘房设有不同的温度区。这种设计有利于工件通过不同温度区,逐步去除挥发性物质,防止溶剂斑和水迹产生,使漆膜达到**佳流平,得到外观优良的漆膜。
三、阴极电泳涂料(CED)基本参数
1. 基本物理参数
● 电压(V)
● 电泳时间:电泳时间越长,泳透率越高。 ● 槽液温度(℃):通常为28-32℃
● 电量大小(库仑):电量(Q)=电流(I)×时间(t)
● 库仑效率:每克干漆膜所消耗的电量。该值与树脂中和度和电泳涂料配方有关。 库仑效率=电量(库仑)/干漆膜(g) 或 库仑效率=干漆膜(g)/电量(库仑) ● 电流密度:每平方厘米漆膜消耗的电流(A)
电泳初期,工件外表面的电流密度比内腔的大的多,随着电泳过程的进行,外表面漆膜逐渐增厚,电阻增大,绝缘程度增加,这部分电流密度逐渐减小,内腔电流密度逐渐增加,电沉积在工件内腔进行。由于工件边缘的电场强度较高,电流密度较大,电沉积首先发生在这些部位,随后才进入相邻区域。
电沉积发生在**低电流密度和**高电流密度之间,低于**低值,电沉积不能发生。**高临界电流密度约为10A/m2 ,与此相对应有一个断裂电压。低于断裂电压,电泳才能平稳进行,伴随一定量的气泡(电解水产生)。高于断裂电压,电解剧烈,气泡产生速度极快,将导致电泳过程完全失控,此时发生一连串的连锁反应:高电流引起漆膜温度急速升高,温度升高导致湿膜电阻下降,湿膜电阻下降又引起更高的电流密度,如此往复,**终得到外观极差的漆膜。
● 湿膜电阻:不同电泳时间CED湿膜电阻(Ω)。随着电泳进行,膜厚增加,湿膜电阻RN增加,电流量减少,如下图:
其影响因素有:漆液配方,其中溶剂、基料、颜料和助剂含量都会影响湿膜电阻大小。 ● 槽液电导:电阻倒数,1/R=西门子(S)
去离子水的电导率通常小于10μs/cm。槽液中的离子主要来自于主题树脂及研磨树脂被酸中和后产生的离子,槽液电导主要由这些离子产生,颜料本身产生的离子很少,因而槽液不挥发分越高,电导越高。 ● 槽液电阻:不同温度下槽液电阻。 ● 干膜厚度:单位μm。主要影响因素:槽液温度 溶剂含量 槽液固体分 电泳电压 电泳时间
● 泳透力:涂装工件凹陷内腔的能力,可通过法拉第盒来表示:
包含内腔的工件(阴极)与阳极之间建立电场,电泳首先在工件外表面开始。
增加泳透力的因素有:
更长的电泳时间
工件屏蔽作用小,例如孔洞较多且大 施工电压高
库仑效率高(低C/g或高mg/C) 固体分含量高
CED湿膜电阻高(工件外表面电沉积在断时间内终止,电沉积可以更快进入内腔) CED槽液电导率升高
● 槽液流动速率:电泳槽中槽液流动速率(m/s)
的推移,助溶剂逐渐减少,在这种情况下,MCT曲线向右移动。因此,可以调节助溶剂含量得到所需的**佳MCT,**佳槽液温度及**佳漆膜。
四、CED设备
电泳过程可简单表示如下图:
1. 前处理设备
在CED主槽之前为前处理区好的前处理质量是获得具有优良耐蚀性和附着力漆膜的基础。通常,前处理包括脱脂、清洗、磷化三部分:
脱脂:主要目的是为了除去工件表面的矿物油、润滑油及冲压拉延油以及附着在金属表面的金属屑、灰尘、焊渣、它们是磷化和电泳潜在的尘埃源,可能引起涂膜外观的颗粒;注意脱脂后的清洗效果。如脱脂不充分,一方面易产生黄锈,导致磷化不均匀;另一方面使磷化结晶变粗,涂膜外观变差,耐蚀性能下降。一般在无锈的情况下,可省去除锈工艺,有锈则用除锈剂去除。除锈后清洗干净,特别是夹缝、点焊缝等处易残留除锈剂(一般为无机酸)。 表调剂由金属钛盐组成,它能沉积在工作上形成磷化膜的结晶中心。表面调整和表调效果的好坏,直接影响磷化膜的状态以及磷化膜的结晶大小。
磷化:磷化方式:浸渍型和喷淋型磷化膜特征:· 外观:均匀、致密的灰色膜,无条纹、花纹式杂色斑痕· 电泳失重:≤8%· 结晶大小:5~10mm · 膜厚:2~5mm· P比:≥85%(喷淋型膜P比略低) #p#分页标题#e#
去离子水洗:清洗用循环去离子水,水质电导率≤100ms/cm新鲜去离子水洗的水质≤25ms/cm(**好10ms/cm以下)**后一道去离子水洗后的滴水电导率应≤30ms/cm 滴水取样法:离开**后一道水洗区后**下一道工序(风干或电源)间滴落的水,以判断工件的水洗状态。磷化膜表面的磷化沉渣应尽可能地洗掉。 2. 电泳槽
CED电泳涂装线包括漆液循环系统、阳极系统、超滤系统、清洗系统、加料系统以及直流电源等六大部分组成。
● 漆液循环系统
阳极液变化及调整:
阳极液电导率太低: 可能去离子水加多了,将引起膜不足,可用添加剂进行调整; 电导率太高: 将导致漆膜过厚,施工电压下降,
可排放部分阳极液及补加去离子水进行调节; 阳极液混浊: 由阳极罩渗或阳极膜破裂导致,应进行检查, 关闭阳极罩,断电进行修理; 阳极液不流动: 可能由于泵坏或管道及阀门堵塞引起, 应对系统进行净化;
阳极液“长毛”: 由菌类形成,应用化学药品如H2O2等进行杀毒和清洗。
2. 除去电泳漆工作液的杂质
3. 加速新溶液熟化和控制工作液中的溶剂含量 4. 电泳漆的回收利用
除杂是超滤机**有用,**主要的功能,因为大多污染物是以可溶性盐形成带入工作液的。它们危害工作液:大多数阴离子(尤其是氢氧化物和铬酸盐)易与漆形成沉淀物:阴离子会降低漆在工件表面的沉积速率并使漆外观变差。超滤机能有效除去这些污染物,起净化作用。电泳液不宜过量超滤。否则会损失电泳漆的主份和降低溶剂含量以及改变电泳漆的酸度。只有新配电泳漆时,才过量超滤,以除去过量溶剂和小分子合成物。
● 清洗系统 1.槽上冲洗
除去电泳漆膜表面附着的浮漆,保证涂膜外观 工件(车身)露出电泳槽后要在1min内进行清洗 2.人工辅助冲洗(包括喷淋和浸渍冲洗) 3.清洁的去离子水清洗
3. 烘烤固化设备
被涂工件先在100℃下预烘烤约10min ,再加热到150-180℃(工件)下保持25-30分钟。固化时,封闭的异氰酸酯解封发生交联,漆膜由于封闭剂损失会发生部分收缩。烘烤效果:用MIBK(甲基异丁基酮)擦试,往复十次,擦布上应不染色,被擦的漆面不模糊失光,说明固化已充分。
五、检测项目
● 槽液固体份测定(NV)
固体份是指电泳涂料在105℃时加热3小时后,剩余的干燥树脂和颜料份的百分含量。测
电泳涂装场合的颜基比是指电泳涂料、槽液或者涂膜中的颜料和基料(树脂)之比。颜基比的测定有溶剂法和测灰分法。电泳涂料所用的颜料,除碳黑外一般都是不燃性的无机颜料,因而常用测定灰分来算出颜料份,方法简便。 1) 检测仪器和材料
①.坩锅和马福炉 ②.恒温干燥箱 2) 测定方法
①.称取定量(10g左右)的漆样或槽液样于已称量的坩锅中;
②.在110±5℃下烘干1小时,随后在200~250℃下烘1小时,再在400~450℃烘0.5小时,再升温**800℃煅烧0.5小时;
③.冷却后将坩锅重新称量; ④.计算:
灰分=(C-A)×100/{(B-A)×(D/100)} 颜基比(P/B)=(C-A)K/[ D(B-A)-(C-A)K]
式中:
A 坩锅的重量(g) B 坩锅加试样重量(g) C 煅烧后坩锅加试样重量(g) D 漆样固体份(%)
K 为碳黑修正系数,在黑漆中K为1.15。
● pH值的测定
测定pH值,可采用一般pH计。测定前,先按pH计的说明书校准pH计。测定温度控制在25℃。其中槽液、极液、超滤液、去离子水可直接取样测定,而乳液和色浆则必须先用去离子水稀释一倍后再测定。 ● 电导率的测定
电导率的测定可采用一般的电导仪测定。注意温度控制在25℃
六、阴极电泳涂料可能出现的问题及解决方案
HED系列阴极电泳涂料在施工过程中,尽管在规定的工艺参数下实施监控和管理,但由于各种相关条件的影响,仍存在出现问题的可能性。为了方便用户的使用,我们特把易发生的问题,产生的原因及解决方法列表如下:#p#分页标题#e#
七、阴极电泳涂料投槽方法及注意事项
1. 单组分ST-2阴极电泳涂料投槽方法
投槽前需对设备进行调试,确认各设备运转正常,然后进行彻底清洗,消除油污、积垢等杂质。
ST-2阴极电泳涂料为单组分、高固体份(68%—70%)、高粘度阴极电泳涂料, 投槽应采用加水逐步稀释的方法。
以4L电泳槽为例,配槽步骤如下:
称取原漆1kg,置于干净的电泳槽内,另称取3kg的去离子水。
缓慢向槽内加去离子水稀释,每加一次水均应充分搅拌,使得原漆与去离子水充分混合均匀。每次加水量约为100—150ml左右。
当去离子水全部加完后,将槽液置于搅拌下,充分搅拌熟化24—48hr后进行涂装。 2. 双组分HED系列阴极电泳涂料投槽方法
● 投槽前需对设备进行调试,确认各设备运转正常,然后进行彻底清洗,消除油污、积垢等杂质。
● 根据槽液配比(乳液:水:色浆=4:5:1)准备好物料,将去离子水加入到电泳槽中,在搅拌状态下,加入乳液;
● 在色浆中加入适量的水搅拌均匀,然后缓慢加入到电泳槽中,边加边搅拌; ● 充分搅拌熟化24小时以上;检查测定槽液的各项指标:pH值、电导率、固体份。 3. 注意事项
在建浴完成后必须保证充分的熟化时间(以48hr为佳)。方可进行涂装。